CAE and Simulations
The process of industrial design and analysis now completely relies on computer simulation, which is founded on numerical analysis of structures, fluids, acoustics, and other fields of study. The automakers have been able to improve the efficiency, convenience, and longevity of the vehicles they create while simultaneously reducing the time and expense associated with the product development process. In order to replicate the behavior in a manner that is as near to the real world as is practically possible, we pretty much use all of the industry-standard software tools at TOOGANN. Our engineers often have a variety of skills, particularly in regard to their competency with software, and this provides our customers with the adaptability that they are searching for.
CAE and Simulations Process
Your design will progress via a significant number of iterative revisions as you develop new and improved products. You need to be able to make educated guesses as to whether or not the proposed enhancements will have a positive or negative impact on performance in the real world. The use of computer-aided engineering simulation provides engineers with the ability to look into the future and determine how the functionality of their products will be affected by any changes made to the product's design.
When properly implemented, it may be used to enhance your design over several iterations, offering data to drive the process of designing anything from its earliest phases all the way to production and possibly even further. This package features the best-in-class simulation tool that can be found in any industrial Computer-Aided Engineering (CAE) tool. It also delivers the most extensive set of physics models available. If you model the physics of your product using an approach that makes no concessions, you can be certain that your predictions will accurately reflect the real-world behavior of your product across the entirety of its operating range.
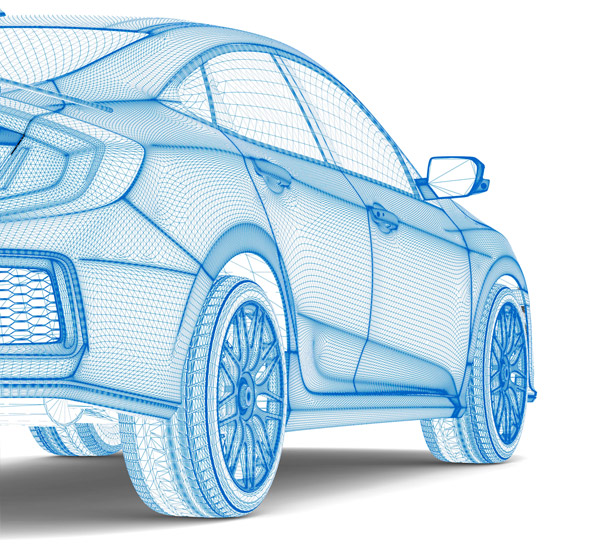
Types of analysis
The following types of analysis are some of the many possible applications for CAE simulation:
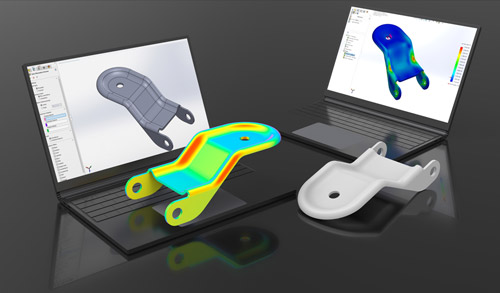
Structural Analysis
An object can be subjected to either static or dynamic loading, and structural analysis will determine the stresses, strains, and deflections caused by the loading (changing as a function of time or frequency).
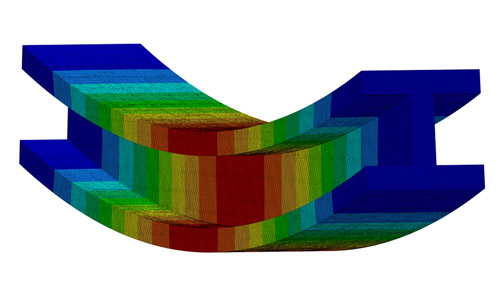
Modal Analysis
The inherent frequencies of an object, as well as the forms of its modes, can be determined using modal analysis. Having knowledge of these modes allows one to prevent resonance brought on by surrounding vibration sources.
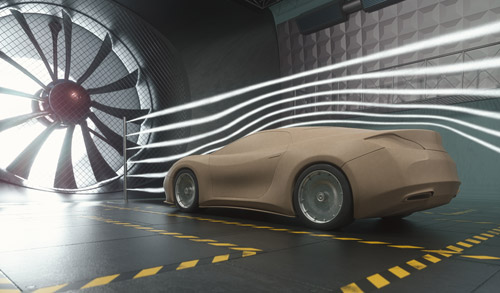
Thermal and Fluid Analysis
The processes of conduction, convection, and radiation are all accounted for in the temperature and heat flux calculations made by thermal analysis. Both steady-state (when everything is in balance) and transient analysis are possible here (over time).
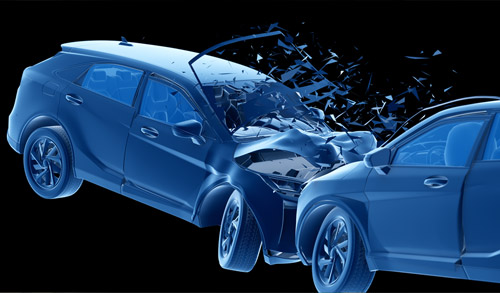
Safety Analysis
Vehicle Crashworthiness is an important aspect of occupant safety. Crash mitigation design that can lessen its severity can be possible analyzing vehicle structure for various crash modalities.
CAE Benefits
It is possible to significantly cut down on the cost and amount of time required for each iteration of the design process, as well as the overall development process, by making use of the benefits offered by engineering simulation, in particular when combined with the power and speed offered by high-performance cloud services. The typical workflow for CAE begins with the generation of an initial design, followed by a simulation of the CAD geometry. After running the simulation, the results are analyzed, and this information is used to make the design better.
This method is iterated upon until all of the product's requirements are satisfied and can be considered practically confirmed. In the event that there are any weak points or regions in which the performance of the digital prototype does not match the expectations, the engineers and designers can enhance the CAD model and assess the consequences of their change by running the updated design through a fresh simulation. Because there is no need to construct physical prototypes during the early stages of product development with this technique, product development can occur at a faster rate.